Ignoring supplier risk assessment is like gambling with your supply chain and the stakes are high.
The cost of disruption, compliance failures, and reputational damage can outweigh any initial savings.
On the other hand, investing in proactive risk assessment helps you build a resilient, compliant, and agile supply chain that supports long-term growth.
In this blog post, we'll delve into some practical strategies for supplier risk assessments.

1. Operational Disruptions: Consider a large manufacturing company relying heavily on a single supplier for a critical component. Without a proper risk assessment, they overlook the fact that the supplier operates in a region prone to political instability. Suddenly, an unforeseen crisis halts production, leaving the manufacturer scrambling to find alternatives, missing deadlines and losing revenue.
Fix: Where possible, avoid over-reliance on a single supplier by identifying and onboarding multiple suppliers for critical components across different regions. Regularly analyze the political stability and risks associated with the regions where suppliers operate.

2. Financial Losses: A company enters into a long-term contract with a supplier without evaluating their financial stability. Months later, the supplier files for bankruptcy, forcing the company to pay a premium to onboard an emergency replacement supplier.
Fix: Perform regular assessment of suppliers' financial stability, credit ratings and payment histories. Include clauses in contracts that protect the company in case of supplier insolvency, such as early termination rights or emergency sourcing arrangements.
3. Reputational Damage: A retailer sources products from a supplier who, unknown to them, engages in unethical labor practices. A whistleblower exposes the violation, and the retailer is caught in a PR firestorm.
Fix: Include ethical sourcing and labor compliance requirements in supplier contracts. Prioritize and partner with suppliers that are certified by recognized ethical organizations or governing bodies. In case of exposure, take immediate corrective action and communicate transparently with stakeholders to rebuild trust.
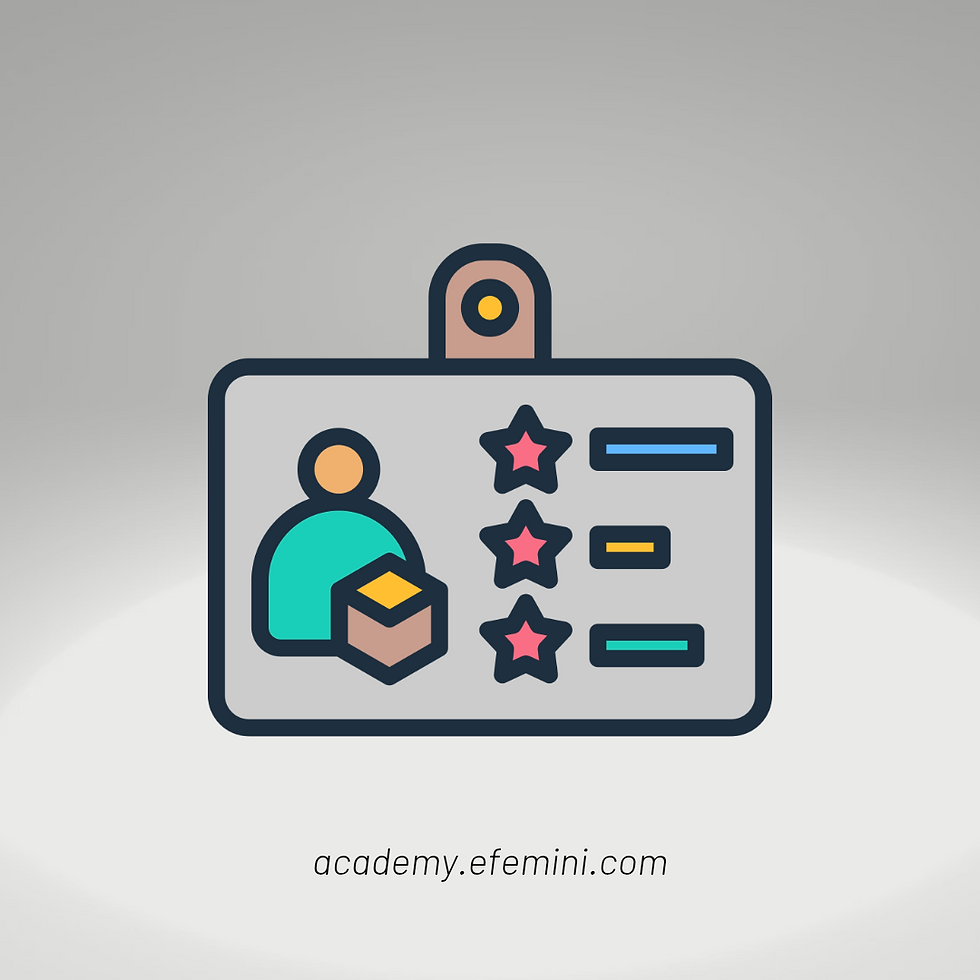
4. Compliance Violations: A pharmaceutical company partners with a supplier that does not meet regulatory standards for materials. Upon inspection, their entire batch of products is discovered to have been recalled.
Fix: Assess suppliers based on their compliance with industry-specific regulations and standards (e.g., ISO, FDA, etc.) Also work closely with suppliers to educate them on compliance standards and ensure they are adequately equipped to meet these requirements. Lastly, be sure to test and inspect materials or products supplied to verify adherence to required standards.
Remember, supplier risk management isn’t just a safeguard; it’s a strategic advantage. Start making informed decisions today and turn risks into opportunities for greater operational success.
Need procurement specific training? Reach out to support@efemini.com and we'll get you sorted.
PS: Join me on 20th February for a Live event on Positioning for Procurement Leadership. Whether you’re aspiring to lead or already in a leadership role, the key to success lies in positioning yourself strategically for the opportunities ahead. Click the link to register and don’t forget to save the date in your calendar!
Comments